

Silo level monitoring systems can help make sure your bins are not overfilled and monitor your inventory, both of which are essential for a grain operation. These wireless bin monitoring systems are less subject to environmental interference and will perform well even in tall, narrow silos thanks to their concentrated beam style of measurement.īenefits of a Technologically Advanced Bin Monitoring System From LCDM However, since sound waves are affected by both moisture and ambient temperature, ultrasonic bin level monitors are not ideal for humid environments or those prone to significant temperature fluctuation.Ī more robust solution, laser silo level sensors require no contact and can accurately detect grain levels at a long-range. These systems are relatively small and tend to be highly cost-effective. The system then calculates the travel time of the pulse to determine the grain silo level measurement.Īnother method of wireless bin monitoring employs ultrasonic sensors to launch and receive a mechanical pulse that detects a level-based density change. The pulse is transmitted down a contact cable or rod, then returns when it encounters the change in dielectric marked by the shift from air to the grain.
#Corn silo height generator#
Silo radar level measurement uses a pulse generator and a grain bin fill sensor to determine the level of solids present in the silo. Today, silo-level radar is a popular method for designing an efficient bin-level measurement tool.
#Corn silo height manual#
Where a silo level monitoring system of the past could have used manual or mechanical methods to determine grain levels, many of the silos used today are massive, making these systems highly impractical. The state of the agriculture industry and the scale of operations in today’s market has demanded more effective tools for grain management. For an affordable price, you can enjoy having comprehensive data on the status of your grain bins. The rotary paddle sensor is a cost-effective choice for those who need bin or silo level indicators. It’s a universal monitoring choice that will likely work for your application.
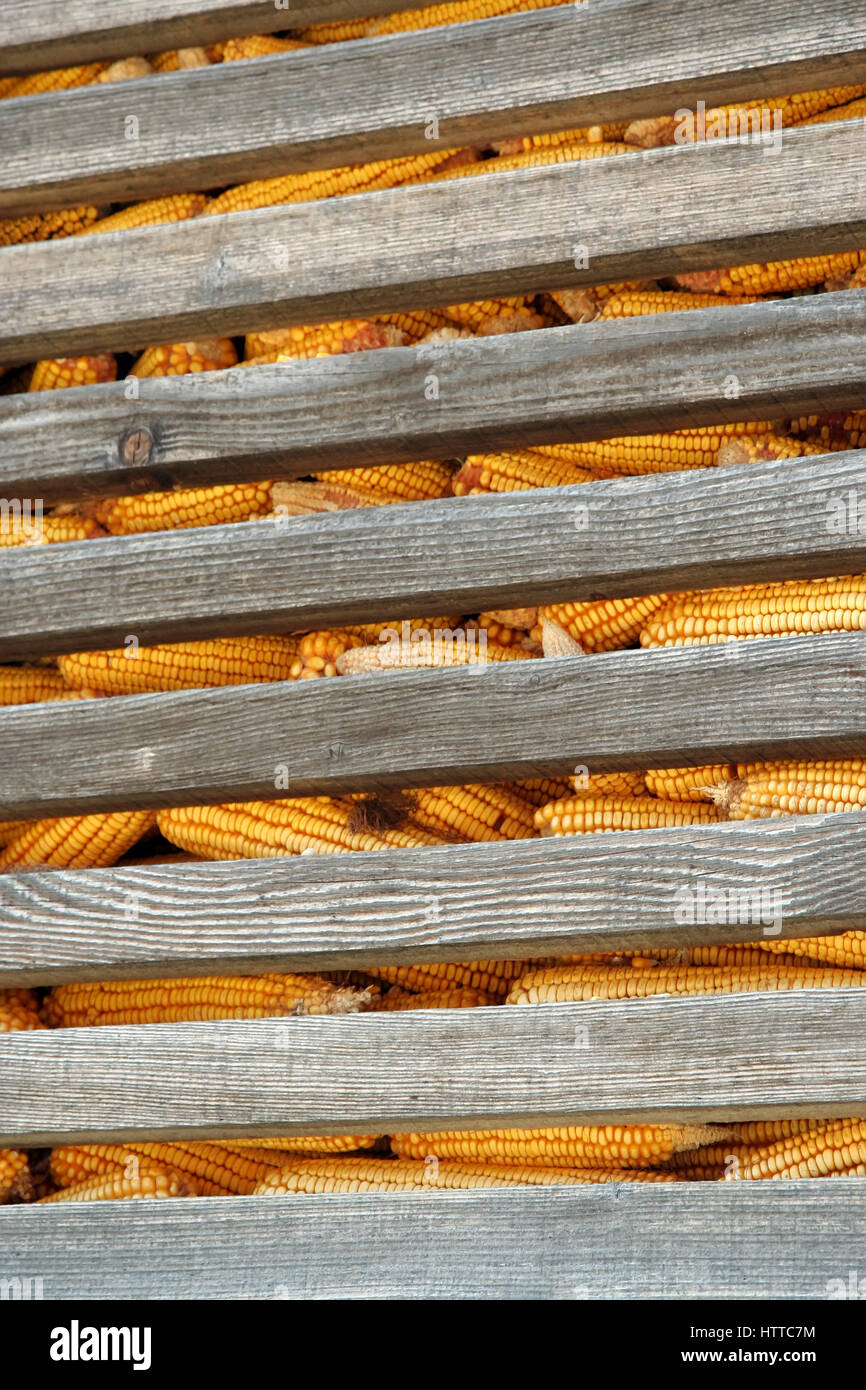
The blue level sensor for grain bins can be used for many kinds of grains as well as materials in other industries. Benefits of Blue Level Sensors Many Applications in Bulk Solids No matter the level of your grain, you can trust that this grain bin level sensor will be accurate every time. When the grain is not there, the motor will rotate to its usual point and activate the switches that cause the motor to turn on or off and change the control output. What makes this grain bin level sensor style ideal is that it recalibrates itself. Both of these statuses will show on the bin level indicator’s output. When the material is present (the grain is at or above the checking point), its weight will prevent the paddles from turning. When the material is absent (the grain is below the checking point), the paddle will turn freely in the air as an indication. These paddles are attached to the shaft, which extends into the bin. The bin level sensor available from LCDM uses rotary paddles, turned by a small synchronous motor, to monitor the bin level. In both cases, you can use a shaft extension to get the rotary paddles to where you need them. It will also mount into the side of the silo for intermediate and low-level monitoring.

You can mount this bin to the top of your silo and extend the shaft down into the silo to your preferred high-level detection point. This bin level sensor will detect materials as low in density as five pounds per cubic foot and as high as 100 pounds per cubic foot. Our blue bin level sensor for grain bins is the ideal solution for an operation with any material that’s free-flowing and dry, like grains and powders. The rotary paddle style of bin level sensor has been used in the industry for more than 70 years because it’s a reliable and effective way to get an accurate indication of grain bin levels. The system of point level monitoring to detect grain bin levels is based on the presence or absence of material in the bin at the measuring point. Industry-Leading Solutions to Bin Level Monitoring
